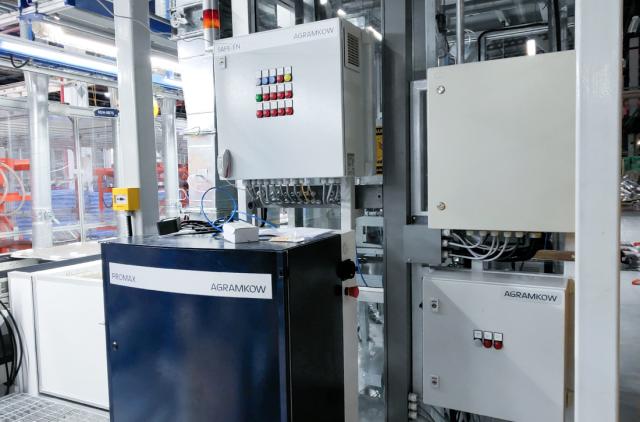
A Complete end-of-line solution for a heat pump dryer production
Electrolux looked to AGRAMKOW as their preferred solution provider for their new dryer factory in Thailand
A complete flammable charging solution with PLIS for a customer in Pakistan
As the demand for cooling equipment such as freezers, refrigerators and air-conditioning is growing, governmental and environmental legislations urge manufacturers to utilize environmentally friendly refrigerants to improve the cooling sector’s carbon footprint.
AGRAMKOW makes it easy for customers to act on climate threat by upgrading their production lines and transform to natural refrigerants. In cooperation with Khan Brothers, a local HVACR & appliance distributor in Pakistan, AGRAMKOW has successfully installed a complete refrigerant charging system for Pak Elektron Limited (PEL) allowing them to reduce their greenhouse emission footprint significantly and at the same time take their production to a higher level with an intelligent production line information system.
Pak Elektron Limited (PEL) is the pioneer manufacturer of electrical goods in Pakistan. In 1956, the Company was set up in technical collaboration with AEG to manufacture transformers, switchgears and electric motors. Until the acquisition by Saigol Group, PEL was solely catering the power equipment market but in 1981 the company ventured into home appliance market as a part of Group’s long term strategy of diversification.
A part of PEL’s mission is to provide quality products and maximize returns for all stakeholders through optimal use of resources. So, when PEL was going to upgrade their deep freezer production line and convert it into using environmentally friendly hydrocarbon refrigerants (R600a), they were also looking for a solution to improve their product quality and production efficiency.
Ever since 1994 AGRAMKOW has been known in Pakistan for quality equipment and together with our partner, Khan Brothers, we have provided high quality service to customers all through Pakistan including PEL.
With PEL’s priorities in mind, AGRAMKOW seamlessly integrated a new equipment into the existing production line allowing them to easily transform to environmentally friendly refrigerant charging. AGRAMKOW installed a complete system solution including safety systems, refrigerant charging system, supply pump and everything that was needed to upgrade the production line.
Furthermore, a production line information system (PLIS) was successfully implemented giving PEL improved access to their data and the possibility for communication between all AGRAMKOW equipment (such as vacuuming, charging, leak detectors, safety and performance tester, etc.) while also supporting third party devices.
In addition, AGRAMKOW completed a training program to assure optimal performance, reliability, and safety during operation. The training program is designed according to industry safety standards to guarantee fully ATEX compliance and for operators, engineers and maintenance team to know how to handle flammable refrigerants and operate PLIS.
Throughout the entire process, AGRAMKOW collaborated closely with PEL as well as Khan Brothers to ensure the best possible solution.
Following the project, PEL is now successfully running their deep freezer production line, charging safely with environmentally friendly refrigerants while having a complete overview of their production line through PLIS.
PLIS has enabled them to have full traceability of every product on their line, they can now determine root cause of defects and delays that has significantly helped them reduce costly errors. They have found opportunities to optimize their processes resulting in improved performance and productivity that has had a positive impact on their bottom line.
Get a glimpse into our world and the solutions we have provided for our customers
Electrolux looked to AGRAMKOW as their preferred solution provider for their new dryer factory in Thailand
With the No-Zone charging solution in place, Vesttherm is now able to charge flammable refrigerants safely and accurately ensuring consistent product quality and higher productivity
The COVID-19 pandemic has created unprecedented conditions, challenging AGRAMKOW and our customers to collaborate in innovative ways
AGRAMKOW makes it easy for customers to act on climate threat by upgrading their production lines and transform to natural refrigerants.